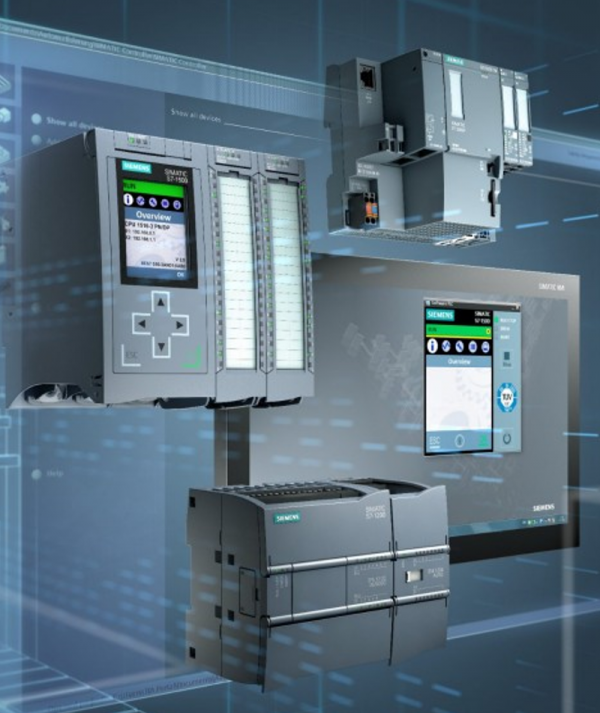
Siemens has sometimes had a reputation of being a high-priced, premium option for CPUs. While we agree that it’s a premium option, we would like to point out three reasons why Siemens CPUs, as part of an automation system, often result in the highest performance-to-price ratio.
1. Many Choices
A wide range of options in Siemens’ CPU line-up allows the user to choose exactly the controller required for the job, without paying for surplus capability.
The Siemens PLC portfolio is designed to ensure the perfect fit. S7-1200 CPUs are ideally suited to tackle all kinds of tasks in smaller automation systems, with built-in IO, integrated safety, motion control and many communication protocols. They are also configured in TIA Portal (The same as all current Siemens PLCs, from all ranges), avoiding the need to learn a separate software package.
The premium S7-1500 CPUs have various IP-rated, HMI, drive-based and standard cabinet-mount form factors. A key highlight is S7-1500 PLCs have an ET200SP form factor variant (Distributed I/O form factor). This has a surprising price to performance ratio offering amazing value, and is the go to CPU for many of our OEMs we distribute to. Within our own project work, in many applications we have found them to be a versatile staple for moderately complex systems. S7-1500 capability ranges up to the ultra-high-performance IPC627 with software controller, supporting 250-axis motion control. CNC Design NZ has experience across the breadth of this range and can help you choose the right CPU for the job.
Siemens safety CPUs offer optimisations in two areas – Firstly, an additional CPU is not required to achieve SIL3/PLe performance, which makes them very cost-competitive with other brands’ safety CPUs. For this reason, our OEM customers prefer to use Siemens safety CPUs instead of standard CPUs with third-party safety controllers such as Flexi Soft. Secondly, all but the two most basic Siemens drive systems support safety over Profinet, meaning no additional wiring is required for safe drive control.
2. Built-in Features
Siemens has taken an ‘extras included’ approach to their CPU offering, i.e. they come packed with features that allow many tasks - that would traditionally require additional hardware purchases - to be handled on-board.
Most CPUs have at least two Ethernet ports on their primary interface, and over half have additional Profinet and/or Profibus interfaces. This allows CPUs to perform network segregation without the need for additional communication modules or switches.
S7-1500 CPUs can host HMI applications on-board using WinCC Unified View of Things. This web-based visualization is accessed over the network from PCs, tablets or thin clients and is ideal for small systems or as a maintenance/backup interface.
A vast array of communication protocols are supported by Siemens PLCs, through either native instructions or application examples created by Siemens. This includes: Secure email, direct SQL connection, MQTT, Modbus, JSON, SNMP, Syslog, FTP, HTTPS, and more. Also, for a small fee, the CPU can be configured as an OPC UA server at the fraction of the cost of a separate server.
3. Compatibility
When talking about cost-effective solutions, compatibility means being able to optimally fit the CPU with the I/O hardware.
Thanks to the Profidrive standard, small Siemens CPUs can control complex Siemens drive systems, and large CPUs can control simple drives with ease. This allows machine builders to select well-fitting components. For example, in a metal forming application that was primarily high-speed motion, CNC Design specified a compact S7-1200 safety CPU along with the top-tier S120 servo drive system for the OEM in question.
Often a make-or-break criteria for system upgrades is the ability to split the upgrade up into several stages. CNC Design NZ has implemented cost-effective retrofits using Simatic motion control because it was possible to re-use existing hardware. For example, for an upgrade to a textile line, all existing servomotors and encoders were kept because it was possible to control them from the new PLC.
Similarly, Siemens CPUs can often interface with old IO systems because they tend to use the Profibus / Profinet communication standards and are supported in TIA Portal.
Conclusion
CNC Design NZ is a Siemens Solution Partner for automation and drives. Operating in NZ for over 30 years and working exclusively with Siemens control systems. CNC Design NZ is ideally placed to specify, supply and support your Siemens parts throughout their life cycle. We can offer a PLC system for every need. Contact us to discuss your next machine development or automation project.