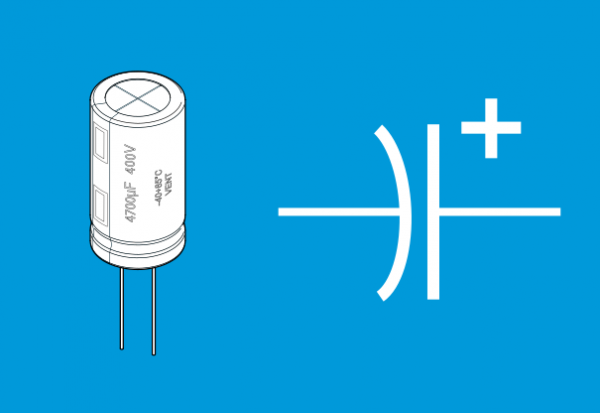
Have you planned ahead and invested in spare servo or VSD drives on your shelf, to get yourself up and running ASAP in case of breakdown? If yes, that’s brilliant self insurance against extended machine downtime, giving valuable peace of mind for that 3am breakdown.
How
ever, did you know that un-powered drives need maintenance? If your drive has not been powered up for a certain number of years, the electrolytic capacitors within them should be ‘re-formed’ before enabling them to run a motor. Otherwise the drive may fail immediately, or prematurely after installation. Have you ever had the situation where your industrial service engineer or electrician says they had to swap drives several times from spare parts stock, before they got one that worked? Empirically that was likely because they had been on the shelf for more than a year (VSDs) or two years (servo drives) and not had their capacitors reformed.Modern drives from any vendor almost all contain electrolytic capacitors across their internal DC bus, so this is a topic for both Siemens and 3rd party drives. While electrolytic capacitors don’t have a charge against them, the dielectric layer separating the positive and negative regions of the capacitors slowly thins. Once a critical point of thinning is reached, if one enables the drive there is a significant risk that the dielectric layer will fail and the capacitor/s short out, rendering the drive inoperable.
For example, for Siemens G120, G120C, G110 or Micromaster VSD/general drives, if more than one year but less than two years has passed since the manufacturing date, they should be connected to the line supply for one hour before enabling them. If more than two years since manufacturing date, the voltage across the capacitors must be slowly stepped up along a scheme outlined in their respective manuals. If done manually, this is time consuming labour wise; timing how long the drive should be at each voltage step, then changing it as appropriate.
Fortunately, CNC Design’s service department offers a drive forming service which is automated. This is yet another arrow in the quiver of our Siemens automation and drive service offering we have built up over 33 years in New Zealand. We have an inhouse programmed Simatic PLC, Comfort Panel HMI and associated voltage step switching equipment (Via a light bulb based load bank) to automatically step up the voltage. On the HMI one selects the Siemens drive model, then input it’s serial number. The Simatic S71200 PLC on the service rig then calculates the drive age from the serial number, and sets the correct voltage steps for the correct time, based on drive model and time since manufacture.
If you have a non-Siemens drive, or a drive that has been powered on or previously reformed since manufacture, these cases are catered for by the HMI’s manual reforming interface. Within this interface a bespoke capacitor reforming scheme can be configured.
As well as the VSDs, we regularly reform Siemens Sinamics S120 and Simodrive 611 servo drives. These drives only need forming if they have not been powered on or formed within the previous two years.
The legacy Siemens Masterdrive is also a semi-frequent visitor to our forming rig.
In addition to complete drives that we form the capacitors on, we also form replacement capacitor banks external to the drive for Masterdrive or Sinamics cabinet size modules. This is a more manual process.
Regarding your spare drives on the shelf: If you want to use those drives immediately in case of breakdown at your factory (sometimes the reforming process can take many hours for quite an old drive). They should be formed every year (VSDs) or every two years (Servo drives). CNC Design offer this as a paid for service if done proactively as part of your preventative maintenance procedures. Depending on the number of drives, we can offer a sliding discount. By reading the manual for your respective drives, you can certainly do this yourself. But if you want to off load this task, give the CNC Design sales team a call – referring to this article.