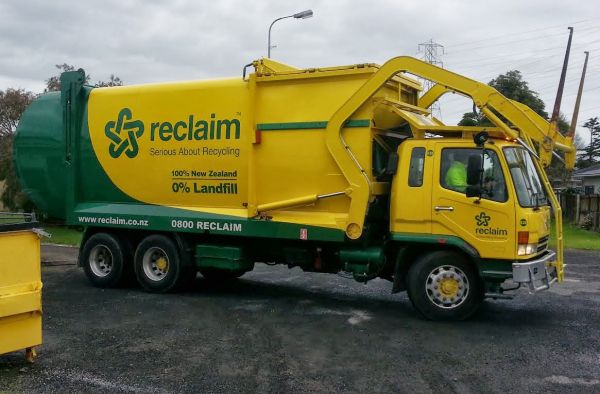
A new Siemens controller installation from CNC Design ensures trouble-free performance and enables remote smarts on a press at Reclaim’s Auckland recycling plant.
New uses for old waste
Operating since 1975, Reclaim is New Zealand’s largest privately owned processor of recyclable materials, helping to divert waste materials away from landfill and into new uses. With its main centre in Penrose, Auckland, it has offices also in Wellington and Christchurch, ensuring nationwide coverage.
Each month, Reclaim collects around 900 tonnes of glass bottles and jars, 7000 tonnes of card and paper, and 350 tonnes of plastics, all of which are later recycled into new products and materials. The business also handles food, residual and green waste, and manages secure destruction of confidential paper waste.
The team at CNC Design support Reclaim with the maintenance of their Siemens PLC equipment.
CHALLENGE
Controller faults lead to downtime
At Reclaims’s Auckland centre, Lindemann hydraulic presses are used to compress paper-based waste into bales. When the programmable logic controller (PLC) on one press began playing up, leading to periods of unplanned downtime, it was time to upgrade, as Dave Carrick, Reclaim’s Head of Engineering and Maintenance, explains.
‘The controller, a Siemens S5 model, was 25 years old, with a large set of input/output cards, which are like big circuit boards. If an I/O card isn’t working, the machine stops. Replacement cards are as rare as hens’ teeth, and downtime can cost us $1600 an hour in productivity – so it’s critical we keep presses operational. Most of them are running at least 40 hours a week.’
FIGURE 1: The Lindemann Paper Press, with compressed bails of paper and cardboard leaving the press
SOLUTION
Upgrading essential
Reclaim had used our services before, always with good results. And when this upgrade came up, we showed them how we had done it successfully before on the Interislander ferry.
Since the S5 was no longer supported by Siemens – there were no software updates or new parts – we recommended that Reclaim upgrade the controller to the Siemens Simatic S7 1500, which is locally stocked and runs the latest software. Also, with its TIA (totally integrated automation) portal, the S7 1500 – and any other equipment it communicates with – can be operated from a single interface. That allows the controller to be linked to the cloud and operated from anywhere, vastly simplifying fault-finding.
PROCESS
Quick connect system makes it simple
Dave had concerns about the risks associated with the changeover. ‘We’d heard horror stories from Europe where jobs like this had caused a fortnight’s downtime. At the very least, we expected two offline days for the job.’
We used our quick-connect system which meant that there was no need for re-wiring. We removed the I/O cards and replaced them with pre-wired connectors, minimising the risk of any wiring issues. And because Reclaim was staying with Siemens, there were no software code issues.
‘It was a huge relief,’ says Dave. ‘CNC copied the old program, rewriting it to suit the new system, and must have got it 100% right. We got rid of all the I/O cards, which are now spare stock for the other machines – though they may be upgraded at a future date, too. And the new, state-of-the-art PLC needs fewer spares, unlike the old system, so it’s a much simpler setup for our engineers.’
IMPACT
Remote access a plus
With the new controller, the Lindemann press is fully optimised. ‘It’s run without incident,’ says Dave, who explains that it is also set up for a fully adaptable, low-maintenance future.
‘We will eventually relocate the press to our Wellington plant. And because we can add a modem and remote dashboard control to the S7, our technicians can still diagnose any faults from Auckland and help the Wellington team fix them fast. It’s a simple case of reading error codes, which tell us where the fault is – hydraulic, electrical, mechanical. The remote operation is an add-on cost, though, so we’ll action that when it’s time to move the press south.’
With breakdowns, our team work with our customers’ industrial electricians to resolve the issue. But when old controllers fail, it’s time to take stock of their equipment and make recommendations for change. In this case, Reclaim wanted diagnostics, screen capability, the option of connecting remotely. With the quick-connect system and the agile setup, we’ve resolved Reclaim’s issues and set them up flexibly for future productivity.