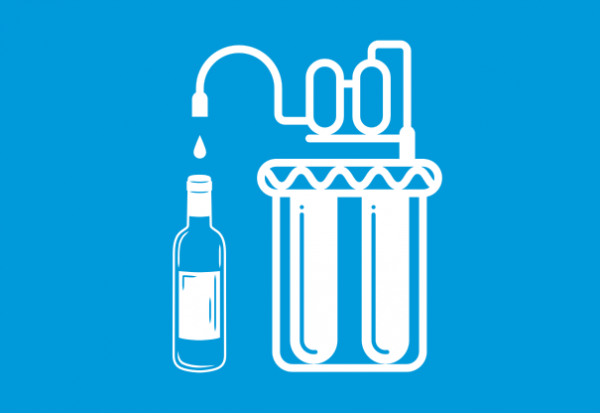
A Human Machine Interface (HMI) failure on a cross-flow wine filtering machine, who’s OEM had closed down, causes owner headaches.
The original machine dealer referred the machine owner onto CNC Design due to their confidence in New Zealand’s only sole dedicated Siemens NZ industrial automation equipment distribution, engineering and Siemens industrial automation service house to bring the machine back to life.
An aging and obsolete Siemens TP177b touch screen failed to boot, rendering the machine inoperable. No backup data existed and the Italian OEM responsible for the machine had closed down and hence unable to provide any support or code for the machine. As a result, CNC Design was approached to reverse engineer the HMI and restore the machine's functionality. This was a cheaper and faster alternative to purchasing a new beverage filtering machine, especially with the hardware lead times and operator training a new machine entails.
Reverse engineering the HMI was a challenging task. As there was no access to the original HMI configuration, or commented PLC source code that the Simatic HMI communicated with. The team at CNC Design extracted the machine’s PLC code and systematically analysed it in order to understand how it interacted with the HMI. The HMI was recreated using a combination of the customer’s knowledge of the machine's operations and CNC Design’s expertise in programming Siemens NZ systems, and understanding of best practices for industrial HMI development. This new HMI configuration was then loaded into a modern Siemens TP700 Comfort Panel, which has an interface to communicate with the older Simatic S7-300 PLC via Profibus. The Comfort Panel was engineered in Siemens’ Totally Integrated Automation (TIA) Portal automation engineering platform.
This process consisted of three main parts.
1. Comprehensive analysis of the machine.
CNC reviewed the machine manuals and interviewed the operators to gain a complete understanding of the machine's functions, work flows and operational limits. The cross-flow machine's design, including its hardware and software was studied, to identify how the Siemens HMI was interfaced with the PLC and the data flows required. CNC planned which crucial functions to restore first and a subsequent path to restore full functionality to the system.
2. Recreate the screens graphics.
Machine manuals were consulted which contained screenshots of the original HMI screens. The screenshots were analysed to understand the layout, features, and functionality of each screen. Using this information, new screens were created with the same look and feel to the original. This enabled CNC Design to ensure the operation steps of the machine were unchanged and that all necessary features were included. This approached ensured the cross-flow machine looked and performed as before, preventing the need for time consuming and costly operator training.
3. Link all screen functions to the correct code variables.
The Siemens Simatic S7300 PLC code was uncommented and written entirely in Structured Text Language (STL), which made variable linking a difficult task that required deep expertise and experience with Siemens NZ PLC programming and industrial automation best practices. A methodical approach was essential to ensure no features were missed and all HMI inputs and outputs were linked with the PLC correctly. A thorough testing procedure ensured all interfacing between the HMI and PLC was correct.
The reverse engineering the HMI for the customer’s cross-flow wine filtering machine was a challenging but successful process. The control systems engineers at CNC Design were able to systematically analyse the machine's process design and operations, and recreate the HMI using their knowledge and expertise. This project was another in a long line of 32 years of projects illustrating that CNC Design can use their extensive experience with Siemens NZ PLC programming and industrial automation hardware to reverse engineer code and retrofit machines for customers with specific needs or cost constraints. Such retrofits have been proven to result in minimal downtime and result in increased reliability, serviceability and future proofing of a myriad of machines for years to come.